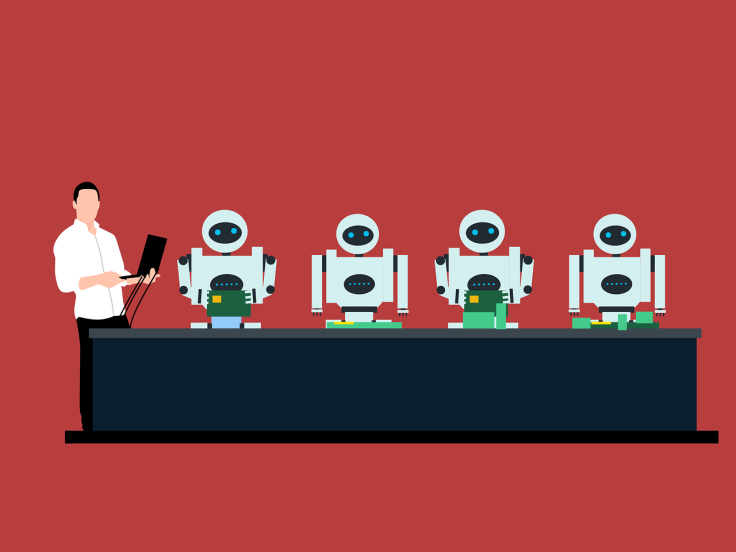
Customer satisfaction is and always will be the benchmark for businesses and is something the manufacturing industry is warming up to. It's achievable only when field services are of the highest quality and laden with new technology. With the field service management market valued at $29.9 billion by 2031, its influence is widespread throughout the world.
Most companies face the following challenges in field service, which directly derails manufacturing operations:
• Shortage of raw materials and spare parts
• Disorganized inventory management system
• Proper disposal of waste and the expenses of doing the same
• Ineffective service management
• Adequate usage of manufacturing management software.
The promising side of field service is that it can act as a catalyst in automating workflows in the manufacturing business. By promoting new technology like manufacturing management software, manufacturing businesses can improve their working styles and task completion times and give a modern makeover to the company.
6 reasons why manufacturing businesses need field service management software
Every other business is upgrading to better solutions that will help their company grow and be successful. One of those solutions which is majorly used, even in discrete manufacturing, is field service management software. Experts built the solution to automate workflows within the company and provide end-to-end results to everyone associated with the company in any capacity and at any time. When incorporated into manufacturing processes and systems, the following are a few benefits you will get to enjoy.
1. Eliminates paperwork
Manufacturing businesses have a hard time deciding on a particular way of doing things. Most of the time, they use trial-and-error methods to determine results and a lot of paperwork goes into maintaining and recording each method. With field service management (FSM) software, they can record all data by minute on the portal. This will ensure that the information remains intact, secure and accurate.
2. Automates activities
Every company looks for a method to enhance productivity and eradicate repetitive tasks. Similarly, in manufacturing, workflow automation is not far-fetched but possible with manufacturing management software. Scheduling, dispatching, billing and so many more repetitive process are all managed by the software, taking some burden off of the technicians' shoulders.
3. Enhances overall work management
A systematic way of accomplishing tasks is possible when using FSM software. In the manufacturing aspect, it simplifies assigning and allotting duties, handling customer requests and maintaining the workforce and the assets of the company. It can also deal with unforeseen circumstances as the software uses the best features in everything. Overall, work management is essential for the development of the company.
4. Provides accurate data analysis
FSM software not only improves the life cycle of the process involved in manufacturing but also provides accurate data regarding costs and upcoming trends. It continuously reads and analyzes the data stored and updates business owners on better working styles, if there are any. With data-backed decisions, business owners can save on unnecessary expenses and simplify work for their workforce.
5. Updates information for smoother operations
In continuation to point 4, FSM software stores information and makes it easy for field technicians and business owners to access what they need quickly. The information could pertain to customer details, asset information and how-to guides for certain difficult tasks. In manufacturing, this information is crucial as it helps better administration of in-house resources, thereby improving business efficiency.
6. Promotes timely responses
When manufacturing is entirely manual, receiving feedback and suggestions concerning unexpected changes will take a longer time. This will create a huge communication gap between all teams and disturb the synergy within the company. However, with FSM software, companies respond immediately to queries and customers can address their concerns to receive faster services.
Revolutionizing manufacturing with FSM
It is up to manufacturing businesses to decide their holistic usage of FSM services for their operations. The critical factor is choosing the right field service management service that not only enables manufacturers to grow but also promises maximum returns on investment. If you're someone who has just ventured into manufacturing, take time to evaluate which tech-friendly methods suit your processes and wisely choose one that will set you higher than your competitors.
© Copyright 2025 Mobile & Apps, All rights reserved. Do not reproduce without permission.